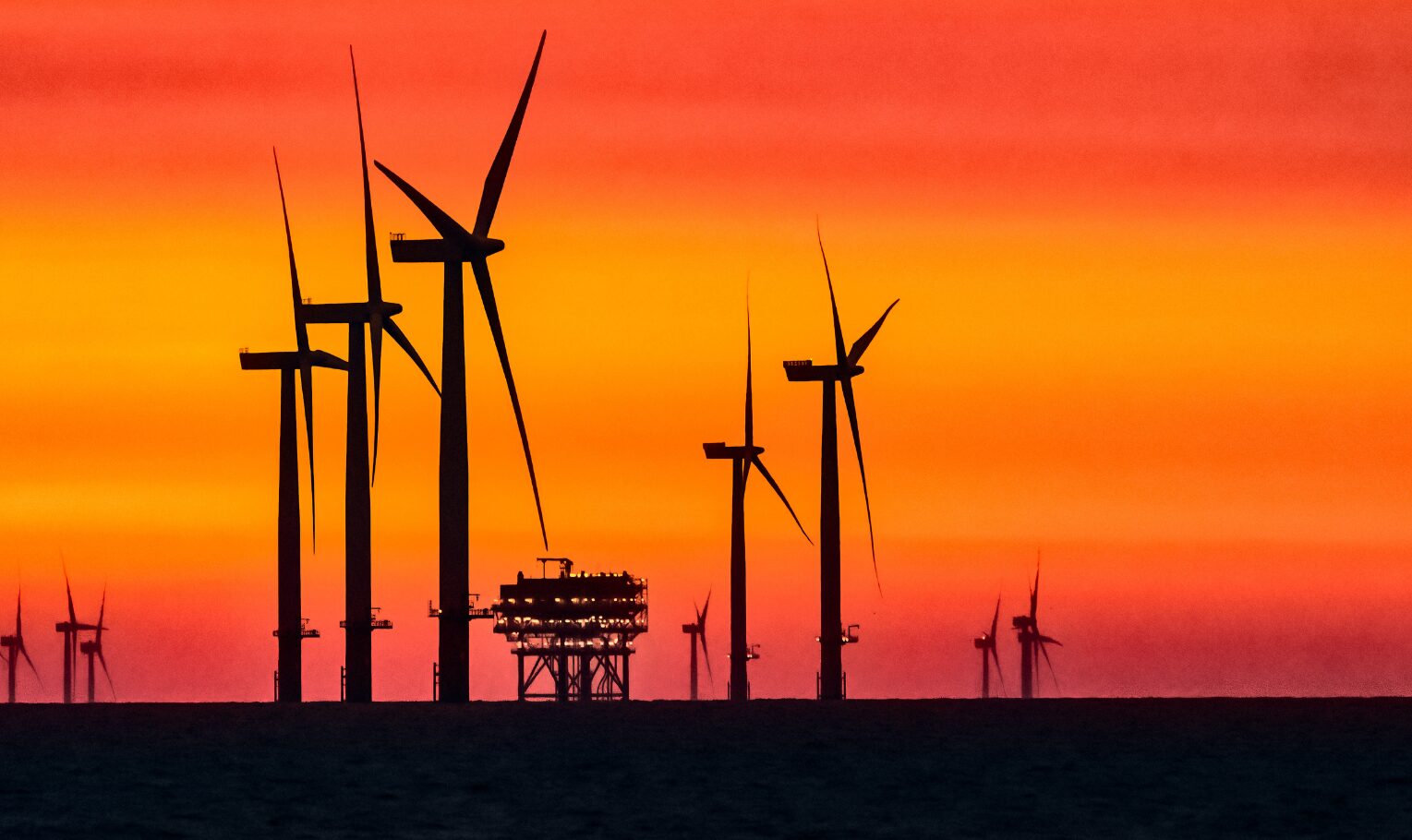
If you want to shift a power-hungry facility to use primarily renewable energy, you’re going to need a battery energy storage system (aka a BESS). The energy produced by solar PV and wind turbines is inherently intermittent, and as a result, the power they provide facility equipment is spotty and unreliable. Unless a buffer is there that absorbs renewable energy and discharges it more steadily, renewables can only be a supplement and another source of firm capacity, like fossil fuels, has to be the base.
In industrial facilities, a BESS can act as that buffer and more. Batteries can provide significant operational cost savings by shaving peak demand energy use and shifting load to use energy when it’s less expensive. They can also replace diesel generators to provide backup power in the event of an outage as well as provide black start capability to recover from a blackout. If the diesel systems need to stay, a BESS can hybridize the system to cover some of the load and reduce wear on the generator.
The potential for BESSs in energy-intensive use cases like industry is huge. Thus far, however, this opportunity has been out of reach to batteries because of the serious fire, combustion and toxic gas dangers lithium-ion batteries pose in hazardous environments such as steelmills, petrochemicals, or oil & gas rigs. But with new high-performance, non-flammable battery technology options entering the arena, these massive energy use cases will soon become viable BESS markets.
Even today, you can see the indications of demand in how these industries are already experimenting with BESS despite the safety concerns. Here are five examples of how industrial companies are leveraging the power of batteries today, giving some insight into what the future may hold as the availability of non-flammable alternatives accelerates:
1. BESS for Powering Data Centers
Data centers require massive amounts of energy to operate. They also depend on having power available 24 hours a day, every day of the year, to avoid serious disruptions to the global data infrastructure. This means that data centers are reliant on diesel backup generators and other redundancies to prevent any interruptions to their operations.
That is set to change, however, with pledges from tech giants to power their data centers with clean energy. Microsoft has pledged to completely phase out diesel power at data centers by 2030 and by 2050 remove all the carbon it has emitted since the company was founded in 1975. Meta, IBM, Amazon, Google and other hyperscale customers have made similar commitments.
Recently, Microsoft replaced the diesel-powered backup generators at its data center in Sweden with battery storage. The installed 24 MW / 16 MWh battery energy storage system (BESS) will displace an unspecified number of diesel generators. It will also support grid stability and provide black start capability to offer rapid recovery in the event of an outage.
Another driver for the replacement was the fact that data center outages can be extremely costly – as much as $1 million for even limited disconnections.
2. Using BESS in Steel and Metal Manufacturing
Steel manufacturing alone accounts for roughly 7% of human greenhouse gas emissions. That’s more emissions than either the European Union or Russia produce on an annual basis, so the imperative to decarbonize steelmaking cannot be overstated.
In metals manufacturing, as in many other industrial sectors, the major appeal of BESS is its potential for lowering operational costs through peak shaving and load shifting to avoid peak demand charges from the utility. That is exactly what Schnitzer Steel Industries, Inc. sought to accomplish when they partnered with Powerflex in 2021 to install and operate a 1.6 MW / 5.5 MWh BESS in Oakland, California. Schnitzer’s Oakland facility processes and recycles ferrous and nonferrous metals, creating both “substantial and variable” demand for electricity. The BESS is configured to charge and discharge in a fashion that reduces the peak levels of consumption, thereby reducing overall peak power demand and cost.
3. Oil & Gas Rigs
The oil and gas industry has taken a liking to battery energy storage systems for a couple of good reasons. When used in a hybrid format, batteries allow operators to reduce the run time of diesel engines and also keep them operating at a level where efficiency is maximized. This extends the life of generators, which usually aren’t designed to handle smaller loads.
Further, battery-drawn energy is available immediately and this improves the dynamic operation of engines, which makes a big difference on off-shore rigs that have highly variable power demand. Incorporating batteries on rigs also offers a much smaller power plant footprint compared to traditional power schemes using gas turbines.
Swedish lithium-ion battery provider Echandia deployed a hybrid system on a jackup drilling rig in the Middle East in 2023. According to the company, the hybridization of the rig will help eliminate peak loads that would otherwise require multiple generators to operate under off-design conditions.
4. Manufacturing of Cement & Concrete
Cement & concrete is a tricky one because most of the emissions come from process rather than energy consumption – i.e. the feedstock materials that release embodied carbon during processing. While alternative, low-carbon alternatives are poised to make the biggest dent in this industry, the potential of BESS in reducing operating costs and managing energy consumption is still very promising.
Building materials group Holcim partnered with TotalEnergies in 2023 to deploy a solar PV and battery storage system at Holcim’s cement plan in Colorado. It is expected to cover around 40% of energy demand at the plant which produces 1.8 million tonnes of various grades of cement per year.
Through the power purchase agreement (PPA) between the two, Holcim will receive roughly 71,000 MWh of power per year. A major function of the battery storage system is reducing the cement plant’s draw of power from the grid during peak demand periods.
5. BESS Usage in Mining & Other Forms of Extraction
Because mining operations, like gas and oil extraction facilities, are often located in remote regions, BESS offers an attractive solution to provide these places clean, reliable power at stable prices. Mining is an incredibly energy-intensive process, with energy expenses often accounting for 40% of a mine’s total operating costs.
In Australia, mining giant BHP and energy provider TransAlta partnered to build a new solar farm in the Northern Goldfields. The project, comprised of two solar farms with 38.1 MW capacity and a 10.1 MW/5.4 MWh battery energy storage system, is stated to help BHP reduce scope 2 emissions at its Nickel West northern operations by 12 percent
The facility is one of the world’s largest off-grid mining solar and battery energy storage systems and features about 70,000 solar panels across 90 hectares of land. The initiative will replace power currently generated from diesel and gas.
With New Solutions, The Future of BESS in Industry is Looking Bright
The outlook for efficiency and emissions reductions in industry by leveraging the power of BESS is encouraging, to say the least. All that’s required to turn the tide in a meaningful way and transcend the limitations of lithium-ion is a new era of high-performance, non-flammable battery storage solutions. To learn more about what Alsym is doing to enable BESS in industrial use cases – contact us today.