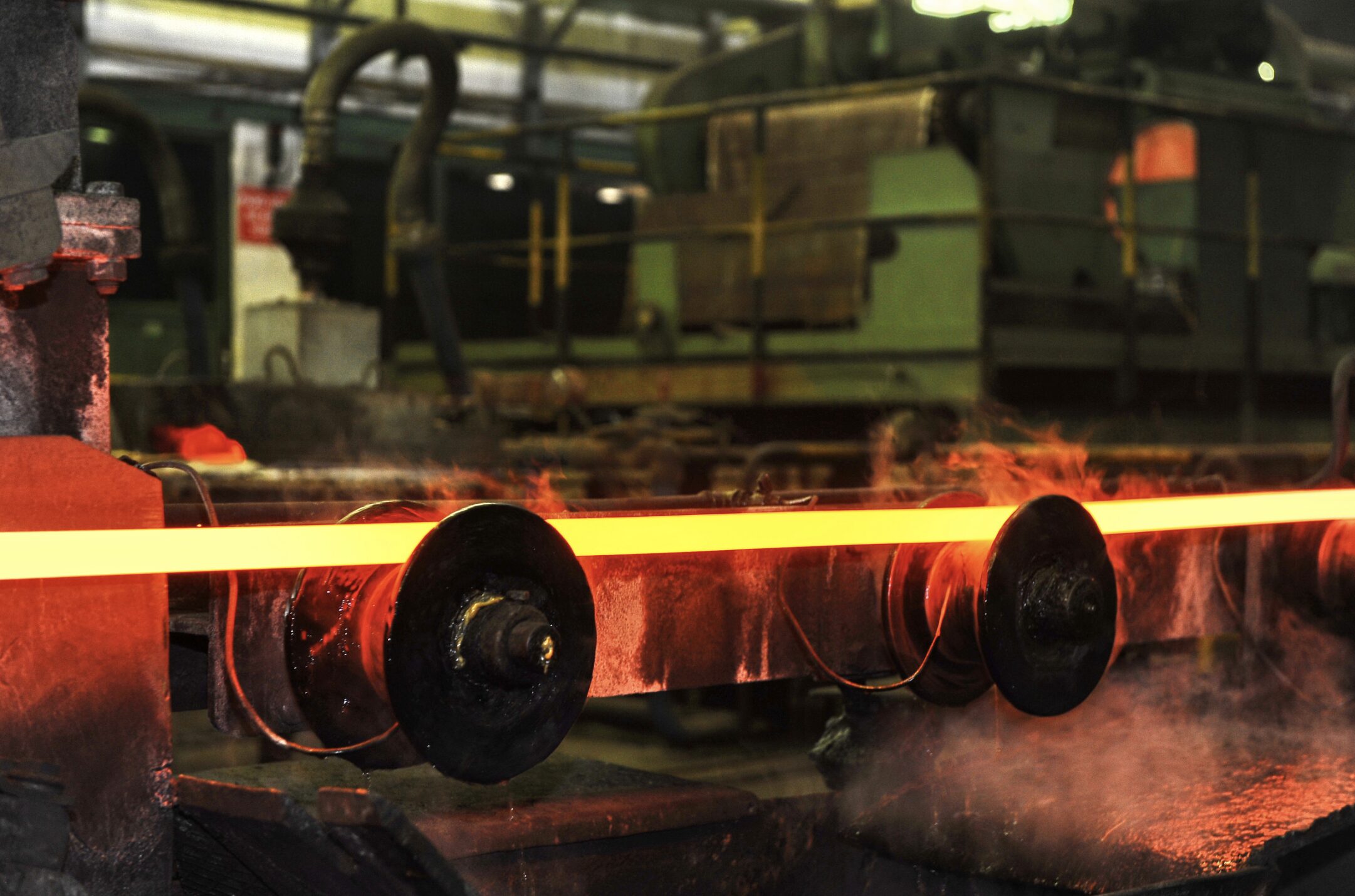
Steel and iron production are energy-intensive processes that contribute significantly to greenhouse gas emissions worldwide. For every ton of steel made, roughly two tons of greenhouse gases escape into the atmosphere. With nearly two billion tons of steel produced each year, there are approximately four billion tons of greenhouse gases generated as a result, accounting for about 9% of human-made emissions worldwide. To put all that into perspective, the European Union, as a whole, accounts for about 8% of global greenhouse emissions.
Decarbonizing the steel and iron industry would make a tremendous impact to global emissions and is an important step towards the Net Zero Emissions by 2050 Scenario developed by the International Energy Agency. Long produced by burning fossil-based fuels to achieve the process temperatures needed, new technological advancements are beginning to turn the tide. Backed by massive investments, these innovations are paving the way for manufacturing facilities to run on green energy for the first time ever.
The Processes of Creating Steel & Iron
Iron has been manufactured using the same fundamental process for thousands of years — expose iron ore to extreme heat to eliminate rust-causing agents, such as oxygen molecules, in a process known as smelting. Steel production takes the process a step further by blending highly purified iron with other components to create an alloy. The additives used in making steel impart properties like flexibility, rust-resistance, and rigidity.
This happens at extreme temperatures of 1600° C / 2900° F or higher and requires the use of refined coal, also called coke. When the coke burns, it releases carbon monoxide which binds with the oxygen molecules in iron, removing them from the ore and generating carbon dioxide.
Greener Ways to Manufacture Steel and Iron
In order to stop producing as many carbon emissions, steel and iron producers need to either find alternative ways to chemically remove oxygen molecules from within iron ore, or to find alternative energy sources to power the refining process. And fortunately, efforts are underway for both.
The use of electric arc furnaces (EAF) as a replacement for basic oxygen furnaces (BOF) – the second super-high-heat step of the steelmaking process – is already becoming relatively widespread. More efficient electric arc furnaces can be powered by renewable electricity to slash emissions. In 2023, nearly all newly announced steelmaking capacity — 93 percent — planned to use EAFs, per the Global Energy Monitor report.
Additionally, governments are getting involved because industry is notoriously tricky to decarbonize. The U.S. Department of Energy (DOE) has allocated $1.5 billion in grant money for companies to find lower carbon alternatives to traditional steel and iron manufacturing. And the DOE’s Advanced Research Projects Agency — Energy (ARPA-E) has offered up another $28 million specifically for more experimental approaches.
Organizations funded by the ARPA-E grants are pushing the boundaries of smelting technology. One recipient is experimenting with reducing the carbon footprint of the process by bathing heated iron pellets in hydrogen to strip away oxygen molecules, eliminating coke from the process. Another is avoiding burning coke by using a fully-electrified microwave hydrogen plasma to create the temperatures needed to melt iron ore in a blast furnace. Yet another company is using acid to dissolve iron ore, then using two electrochemical cell stacks to separate iron ions and create sheets of pure iron, all at temperatures closer to 60° C / 140° F.
Steel and Iron – Forged From..Batteries?
These companies are also reducing their overall carbon footprint by running their operations on renewable energy sources. But because renewables don’t produce a steady supply of energy (solar panels aren’t generating electricity at night, for example), battery energy storage systems (BESS) are needed as a buffer. BESS are able to store energy from renewable sources and distribute it to power plant equipment as necessary.
At adequate scale, battery technology can also help manufacturing facilities lower their operating costs through peak shaving. This is where batteries stop taking energy from the grid during peak demand periods in order to avoid higher electricity rates. This can make a big difference in industrial operating costs, as the power requirements for these facilities is extremely high.
The batteries themselves are also advancing to where they are becoming more suited for industrial applications. Lithium-ion batteries, once the standard for high-volume, short-term energy storage, are being replaced by alternative battery types that are non-flammable, non-toxic, and high-energy. These performance attributes give facility owners an industrial-grade system that can provide safety while withstanding heavy use.
A Long Way to Go
The efforts to decarbonize steel and iron production are certainly encouraging but are a tiny fraction of global production. The relative simplicity of traditional, coke-fueled iron ore reduction and basic oxygen furnaces means that cleaner and greener methods will have to advance to a point where they are well-understood and economically attractive before they can meaningfully penetrate the market.
Battery energy storage systems that effectively manage clean energy will play an important role in the widespread adoption of green smelting processes. As energy from renewable resources becomes more reliable, efficient and cost-effective, industrial manufacturers will find it more attractive than relying on fossil fuels which can be volatile. Batteries are the key to leveraging clean energy and will help reduce costs through peak shaving while also mitigating greenhouse gases, putting the Net Zero Emissions Scenario by 2050 ever closer within reach.