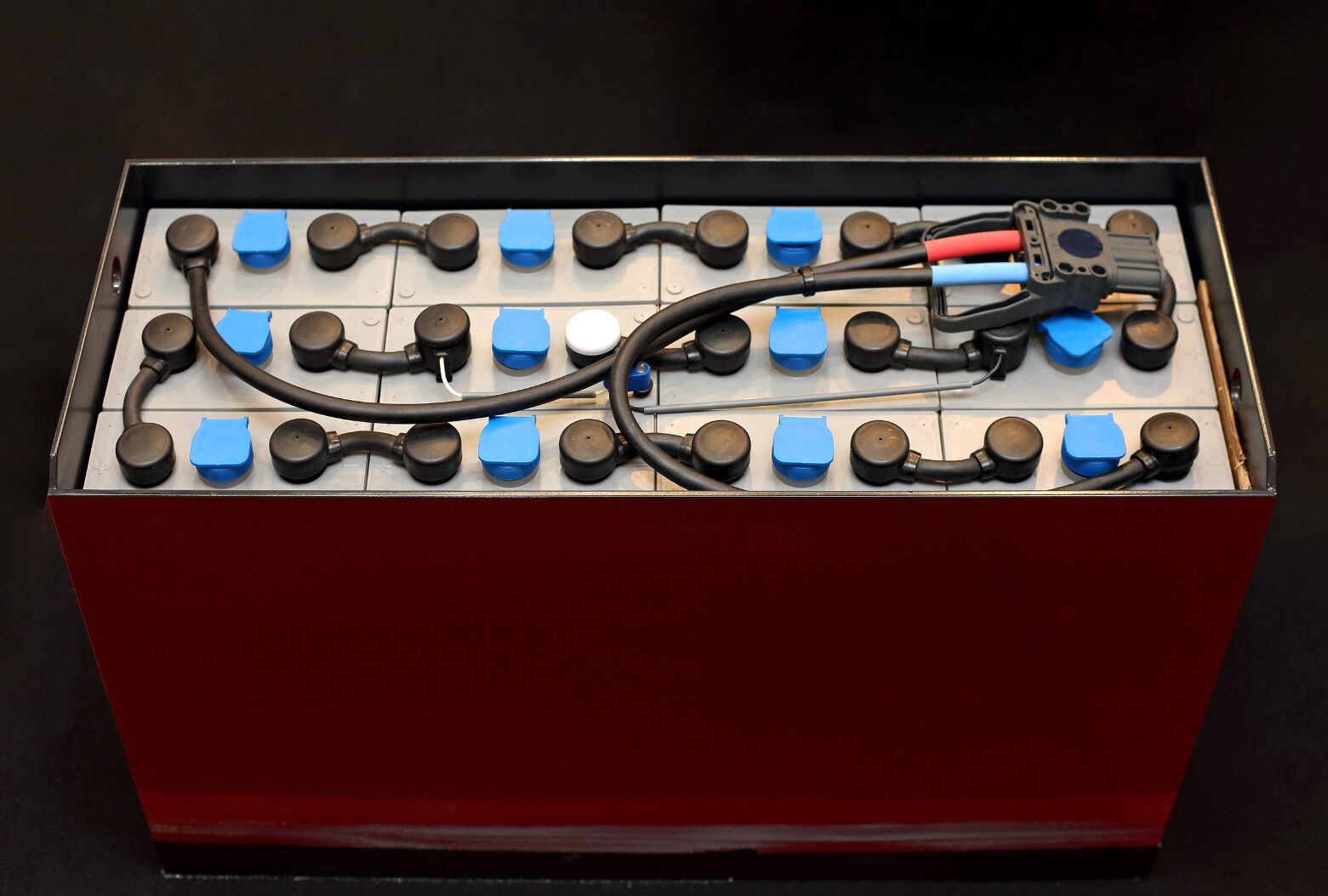
In today’s battery energy storage landscape, lithium-ion runs the show, making up 99% of new energy storage capacity over the last few years. But that is not to say other contenders don’t have a leg up on lithium when it comes to certain safety and performance metrics.
Here we take a look at advantages, disadvantages, and nuances of several newer energy storage technologies vying to get a foothold in the market. For the purposes of this post, the scope of the comparison will be limited to grid-level performance and safety. Let’s dive in.
For each tech, we’ll look at:
- How it works
- Energy density
- Safety
- Cycle life
- Discharge duration
- Other features (low-temperature performance, etc.)
Lithium-Ion
Lithium-ion batteries are commonplace for a couple of reasons. Lithium-ion is a widely adopted, commercially mature technology, used since the 1990’s in consumer electronics and for the past decade in electric vehicles. They work through the well-known, highly efficient intercalation mechanism in which the working ion shuttles between the cathode and anode during charge and discharge. They are also energy dense – up to 700 Wh/L in today’s versions – meaning they can pack more energy per unit of weight or volume than other currently available technologies.
But they have their drawbacks, including the potential for thermal runaway, a relatively high degradation rate, and limited service life in some varieties. Thermal runaway stands front and center of these issues. Several exothermic reactions can occur within the cell due to shorts or abuse that can lead to a rapid and continuous increase in the temperature of the cell. This situation is especially dangerous due to lithium-ion’s use of an inherently flammable liquid electrolyte. The rapid temperature increase of a single cell can affect adjacent cells and lead the entire pack, rack, and system to go into an unstoppable thermal event, resulting in fire or explosion. During these events toxic gases, including deadly hydrogen fluoride, can be emitted. Necessary measures must be taken to avoid thermal runaway; these include intense thermal and energy management, which can reduce energy efficiency.
A relatively high degradation rate (depending on depth of discharge) and limited service life are other considerations that affect grid-level performance. Lithium-ion batteries use a graphite anode that is prone to lithium plating as the battery charges, especially in low temperatures or other thermal transients that compromise the structural integrity of materials and systems.
Sodium-Ion
Sodium-ion batteries operate in a similar way to lithium-ion batteries, but rely on the intercalation of sodium ions (Na+) instead of lithium ions (Li+). They are considered a potential solution to some of the shortcomings of lithium-ion batteries, particularly with respect to safety and performance at low temperatures.
Sodium-ion batteries generally have lower energy density than Li-ion batteries due to the larger size of sodium ions and lower capacity of active materials. Another challenge presented is lack of stability over repeated charge and discharge cycles. The sodium-ion battery sub-technologies on the market today – layered metal oxide, prussian blue analogues, and polyanionic – vary in their active materials and there is no clear winner that can provide high energy density, reasonable cycle life, and non-flammability. The technology tends to be binary: only those with highly flammable organic electrolytes could potentially compete with Li-ion in terms of performance. Those Na-ion batteries with non-flammable electrolytes have significantly lower energy density.
Sodium-ion batteries tend to excel in specific use cases. They have been deployed for uninterrupted power supply (UPS) applications that call for very short-duration high power. They also have much better low-temperature performance than lithium-ion batteries, which makes them useful in extreme northern and southern climates.
With recent manufacturing announcements, sodium-ion will very likely have their place in the market for low-range EVs and perhaps stationary storage. But right now, considering the limitations at hand and because the technology is still in the early stages of commercialization, it will be a while before they are widely used.
Lead Acid
Lead acid batteries have been around and in use since the 19th century. They use lead material in the cathode and anode and a sulfuric acid solution as the electrolyte. They do not use the intercalation mechanism like lithium-ion and sodium-ion. Instead, lead-acid batteries operate through a different electrochemical process involving the conversion of lead and lead dioxide into lead sulfate and vice versa.
Lead acid battery technology has evolved over the last few decades. The three main types on the market today are standard valve-regulated lead acid (VRLA), gel lead acid, and absorbed glass mat (AGM). All have lower energy density than lithium-ion – in the 60-70 Wh/L range – and suffer from relatively short service lives, requiring frequent replacement. Care must also be taken during charging, as overcharging or fast charging lead acid batteries can permanently damage the battery.
Generally speaking, standard VRLA batteries offer higher energy and power density than most other energy storage battery types mentioned in this article but they have a cycle life in the hundreds, reflecting short service life. Failing to properly charge and store standard lead acid batteries can also result in sulfation on the battery plates, causing permanent damage. Leaking sulfuric acid is another possible hazard if the batteries are improperly handled or damaged.
Gel lead acid leverages a gel electrolyte which offers lower corrosion and higher cycle life than standard VRLA, as well as improved safety. However, the unexpected rupture of the battery is still a concern. Gel lead acid is best suited for long-duration, low-power needs.
Lastly, sealed AGM batteries provide enhanced safety because they are completely sealed and the mats holds the electrolyte in place, but they are highly sensitive to overcharging which can and potentially lead to thermal runaway. As the battery gets warmer from the exothermic reaction during charging, AGM batteries can accept a higher charge current, which in turn leads to more heat being produced that damages the battery permanently, and in rare situations could lead to explosion if the safety valves fail. Further, because frequent or deep cycling reduces service life, AGM batteries are best suited to UPS and industrial applications that favor high power instead of extended duration.
Iron-Air
Iron-air batteries are a type of metal-air battery that use iron as the anode and atmospheric oxygen reactions with a catalyst as the cathode, coupled with an electrolyte to facilitate the charge transfer.
Iron-air batteries claim to use abundant and non-toxic raw materials, and present negligible operational safety hazards. However, they have a low round-trip efficiency of 40-50 percent, which could be from inherent inefficiencies or a high self-discharge rate This means a significant amount of the energy required to charge a battery of this type is lost and not available during the discharge of the battery, reducing the amount of energy that is actually stored. If the culprit is high self-discharge, this would make iron-air batteries less applicable for back-up power where the battery needs to hold onto power for long periods until it’s needed.
Further, unlike lithium-ion batteries, an iron-air battery has additional system complexity and balance of plant requirements for the air cathode. This increases the physical footprint dramatically in comparison to other ESS technologies. Additionally, iron-air batteries have a relatively low power density and poor rate capability, which means they are not well-suited for applications requiring rapid discharge. For these reasons, the majority of the capacity of an iron-air battery would only be fully utilized 1-2 times per year, severely restricting the applicability of iron-air batteries.
Flow Batteries
Flow batteries, also known as redox flow batteries, store energy in liquid electrolyte solutions that are kept in two separate tanks. The electrolytes are pumped from these tanks into a cell where they are separated by a membrane. One electrolyte acts as the cathode and the other as the anode, with differing ionic species in the respective electrolytes that can be oxidized and reduced to store and release energy.
This energy storage technology is well-commercialized and offers a high level of safety, long cycle life, and minimal degradation over time because the energy is stored in the electrolyte rather than in solid electrodes (i.e. no intercalation or conversion reactions). Another advantage of flow batteries is that they can be left completely discharged for long periods without suffering any damage, which is not the case with many other types of batteries. They can also offer a discharge duration of milliseconds to 24 hours, which is atypical among ESS technologies.
Flow batteries have some downsides as well. Their energy density is significantly lower than other types of batteries, meaning they take up more space for the same amount of energy stored. This gives them a large physical footprint for practically any energy storage application. They have round-trip efficiencies around 75%, much lower than lithium-ion but higher than iron-air. Flow batteries can also be complex and expensive to manufacture and maintain, as the system involves pumps, sensors, and control units to manage the flow of the electrolyte.
Nickel Hydrogen
Nickel-hydrogen (NiH2) batteries consist of a positive nickel hydroxide (Ni(OH)2) electrode and a negative hydrogen electrode. The battery’s energy is stored and released by the electrochemical reactions of the nickel hydroxide and hydrogen electrodes. During charging, nickel hydroxide on the cathode is oxidized, while hydrogen gas is evolved from the electrolyte on the anode through a hydrogen evolution reaction. During discharge, the process is reversed by acting like a fuel cell (reducing hydrogen gas back to electricity and water).
Nickel-hydrogen batteries have primarily been used for satellite and space applications due to their robustness and a long cycle life to the tune of 30 years / 30,000 cycles under normal use conditions. Discharge durations range from 2 hours to 12 hours, enabling most intraday and interday applications but restricting multiday. The duration is limited by a high self-discharge rate of 30% capacity loss after 80 hours.
Nickel-hydrogen batteries have a lower energy density – particularly gravimetric energy density due to a relatively high weight – compared to other battery types. Their charge-discharge efficiency is also not as high as lithium-ion. With respect to safety, cell components are housed in a tubular high-pressure vessel, which presents safety concerns if cells are punctured or seals fail.
Liquid Metal Batteries
A liquid metal battery is composed of three layers: a top layer with a low-density liquid metal that serves as the positive electrode, a bottom layer of high-density liquid metal that serves as the negative electrode, and a molten salt layer in between that serves as the electrolyte. During the discharge phase, reactions occur at the positive and negative electrodes to form an intermetallic alloy and electrons are released to the external circuit. During the charging phase, an external power supply is used to drive the reaction in the reverse direction, regenerating the original composition of the electrodes.
Liquid metal batteries can operate at high temperatures, which can minimize degradation and enable a long lifespan. Because the system is entirely liquid, it doesn’t suffer from the cycle-to-cycle capacity fade seen in many solid-state batteries. Discharge durations fall between four and sixteen hours.
However, the technology also has some challenges. The high operating temperatures required to keep the metals and salts in a molten state can lead to reduced energy efficiency and presents engineering and safety challenges. The choice of materials can also impact the battery’s voltage and energy density and the use of gravity to isolate the electrodes requires the system to maintain a certain orientation, predisposing it to stationary applications.
Zinc Bromine Batteries
Zinc bromine batteries store electrical energy through zinc deposition. A non-flammable aqueous electrolyte is held within individual cells, creating a pool that provides dynamic separation of the electrodes. During charge and discharge, zinc and halide ions move through the electrolyte to their respective electrode to donate or accept electrons, creating a current flow through the bipolar stack.
Zinc bromine batteries offer a reasonable mix of energy density, safety, and expected service life. Because electrochemical reactions occur on both electrodes during charge and discharge (a bipolar structure compared to lithium-ion’s unipolar), internal resistance is reduced, thereby enhancing service life. But this advantage comes at the cost of slower charge and discharge rates, as well as reduced energy efficiency compared to lithium-ion. Zinc bromine batteries also have a relatively high self-discharge rate of 1 percent per hour which lowers round-trip efficiency and limits the range of use cases. They are best suited for 3 to 12 hour discharge durations. The electrolyte is also toxic which can pose some risk in the event cells are damaged.
How Alsym Is Changing the Game
Alsym batteries are a non-toxic alternative to lithium-ion that avoid lithium and cobalt completely, and use water as the primary solvent in the electrolyte and in the manufacturing of the electrodes. Using readily available, inherently non-flammable materials including manganese and other metal oxides, Alsym batteries offer high performance at lower risk than Li-ion.
Alsym batteries at the grid-level offer the best mix of energy density, safety, efficiency, and discharge duration capability among non-lithium options on the market today. Alsym’s first product, Alsym Green, is targeting system-level energy density up to 3.4 MWh (DC) per 40′ container. Alsym batteries can be used for any discharge duration from 4 to 110 hours, and can recharge in as few as 4 hours. This means Alsym batteries can easily be used for short, medium, and long-duration storage without the need for additional technologies (we call this wide-duration storage). They combine high energy and high round-trip efficiency with a minimal footprint to offer low, industry-leading levelized cost of storage (LCOS). And unlike some dedicated long-duration storage technologies which lose 40% of charge per month, Alsym batteries have high long-term energy retention similar to lithium-ion.
We’re working to make low-cost, non-flammable batteries available to all, in applications beginning in energy storage and evolving into maritime and electric mobility. Contact us to find out more about the future of battery technology.