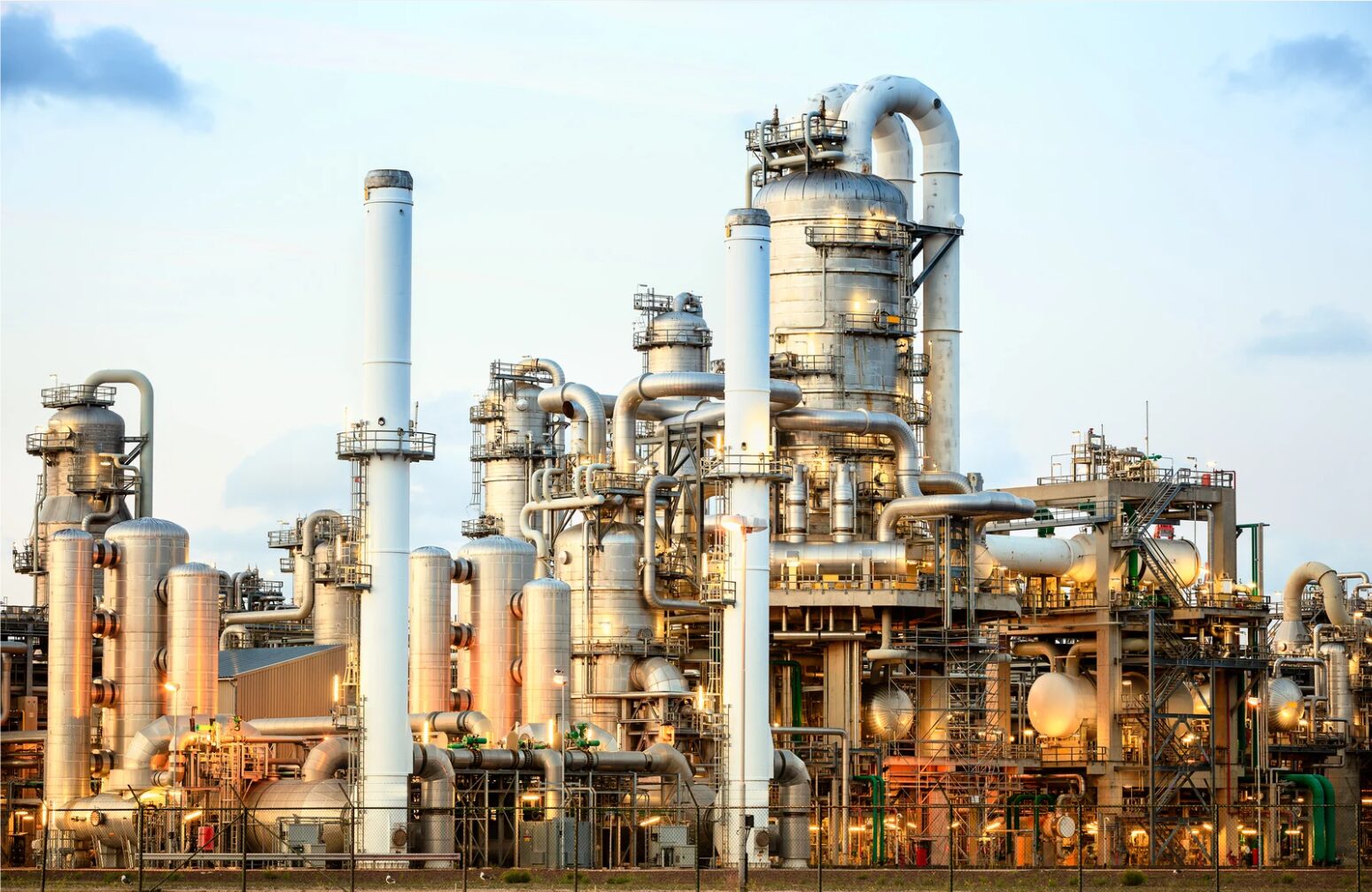
The industrial sector produces 23% of all greenhouse gas emissions in the United States. These come primarily from the burning of fossil fuels, as well as the byproducts of chemical reactions used in various manufacturing processes. By moving to renewable energy sources, implementing advanced battery energy storage systems (BESS), and leveraging low-carbon materials, it would be possible to dramatically reduce the country’s overall greenhouse gas emissions.
Decarbonizing the industrial sector is notoriously difficult to do, but some serious efforts are underway — including a $6 billion investment in green technology by the Biden Administration that will seek cleaner ways to manufacture steel, concrete, and other materials. Huge investments are also being made into the energy storage sector, a market that McKinsey estimates could be worth $150 billion by 2030.
So how will BESS technology and other green initiatives reshape the industrial sector? Let’s look at how batteries can reshape the manufacturing of steel, cement, and chemicals.
The Building Blocks of Decarbonization
Wind, solar, and many other renewable resources can’t provide a steady stream of energy 24 hours a day, making battery technology essential to the clean energy revolution. Batteries are needed to store renewable energy and distribute it evenly — otherwise, traditional power plants based on fossil fuels are needed to fill in gaps in the power supply.
Many industrial facilities have very little operational downtime, which actually makes them good candidates for renewables plus BESS technology because less precision is needed to match times of supply with times of demand. Batteries can give these facilities the flexibility to run off clean energy sources around the clock and significantly lower their carbon intensity.
Batteries in Steel Production
The production of steel requires extreme heat, with temperatures involved as high as 2250° C / 4080° F. It may be hard to believe that renewable resources can satisfy the immense energy requirements needed to produce this kind of heat, and yet that’s exactly how one steel mill in Colorado is already meeting 95% of its annual energy demands. Adoption of electric arc furnaces (EAF) in lieu of fossil-fuel powered basic oxygen furnaces is also opening up opportunities for heat powered by clean electricity. In 2023, nearly all newly announced steelmaking capacity — 93 percent — planned to use EAFs, per the Global Energy Monitor report.
The switch away from fossil fuels isn’t just good for the environment: it’s also good for business. That’s because BESS technology can reduce operating costs by allowing steelworks to charge their batteries during low-rate periods and use this energy when rates are high in a method known as peak shaving.
Batteries in Cement Production
Cement is an essential ingredient in concrete and a fundamental ingredient in countless construction projects. Similar to steel but to a lesser degree, kilns used in cement production require high temperatures up to 1,500° C / 2730° F and this heat is traditionally created by combusting carbon-based materials. Cement manufacturing also releases carbon dioxide through the calcination of limestone, one of its essential ingredients.
This makes cement and concrete production a major contributor to global greenhouse emissions, releasing one kilogram of CO2 into the atmosphere for every kilogram of cement manufactured. Researchers are hard at work to find green alternative feedstock materials for the manufacture of cement. Forward-thinking industrial plants are also beginning to install behind-the-meter BESS technology to shave peak demand charges and power their facilities using renewable resources instead of fossil fuels.
Batteries in Chemical Production
Chemical production accounts for approximately 40% of industrial energy consumption and emissions in the United States, which should come as no surprise considering the massive scope of what these chemicals are used for — plastics, detergents, fuels, adhesives, paints, and countless other compounds for consumer, industrial, and agricultural applications. The chemicals sector is the single largest industrial energy consumer, which is why it’s so important to increase the amount of renewable energy resources it uses.
Unlike the production of steel and concrete, most processes in the chemicals sector take place at temperatures of 205° C / 400° F or less. With this lower requirement, using electrified heat in the form of industrial heat pumps becomes much more viable. The chemicals sector also has a higher percentage of electricity-related emissions (compared to process-related for cement or heat-related for iron and steel), and with renewable energy adoption this electricity can quickly be decarbonized.
Battery systems are therefore vital to reducing the chemical sector’s reliance on fossil fuels. Advances in battery technology allow chemical plants to run on energy from renewable resources without experiencing significant power gaps, and can help chemical manufacturers take advantage of peak shaving to reduce their operational costs while simultaneously cutting their CO2 emissions. The switch to clean energy in the chemical sector will make a huge impact on overall industrial greenhouse gas emissions.
The Key to Sustainable Energy
Battery energy storage systems are the key to breaking the industrial sector’s dependencies on fossil fuels. They overcome the ebbs and flows inherent in using solar, wind, and other renewable energy sources, turning them into viable options for industrial applications. Even standalone battery systems without renewable energy resources can offer an immediate improvement in energy efficiency.
Advances in battery technology are also making these systems safer than ever before. New battery systems are moving away from flammable lithium-ion configurations while preserving high performance, overcoming an important consideration for industrial applications. Switching to battery power means a cleaner, safer, and more cost-effective alternative for industrial processes, and as more and more facilities make the change, it will result in dramatic reductions to global greenhouse gas emissions.