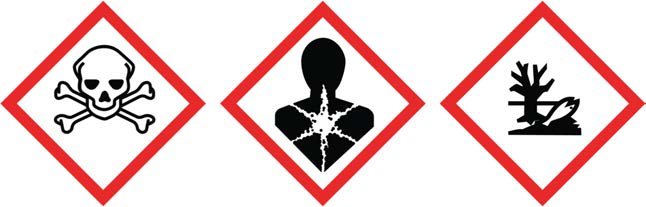
- Written by Dr. Nikhil Koratkar, co-founder of Alsym Energy, John A. Clark and Edward T. Crossan Chair Professor in Engineering at Rensselaer Polytechnic Institute (RPI)
Lithium-ion batteries are everywhere, from the tiny ones in your earbuds to the massive ones in stationary storage installations. And every day, thousands of new batteries roll off the assembly lines—and thousands more find their way into landfills and rivers. It’s easy to assume that these batteries are safe for people and the environment given their ubiquity, but that couldn’t be farther from the truth.
Nearly every metal and chemical process involved in the lithium battery manufacturing chain creates health hazards at some point between sourcing and disposal, and some are toxic at every step. Let’s walk through the most common ones.
Lithium toxicity – Is lithium toxic to humans?
Lithium is used for many purposes, including treatment of bipolar disorder. While lithium can be toxic to humans in doses as low as 1.5 to 2.5 mEq/L in blood serum, the bigger issues in lithium-ion batteries arise from the organic solvents used in battery cells and byproducts associated with the sourcing and manufacturing processes.
Lithium: white gold or fool’s gold?
Much of the world’s lithium is extracted by tapping into underground “brine” deposits, pumping water rich in lithium salts into large evaporation ponds. Approximately 500,000 gallons of brine must be extracted to produce one metric ton of lithium, which significantly impacts the amount of water available for drinking and agriculture in regions such as Chile’s Atacama Desert. Once evaporation is complete, lithium salts are separated from other deposits and sent away for processing. By-products of the brine extraction process can include everything from sulfuric acid and radioactive uranium to lime and magnesium waste, all of which can increase rates of cancer and other diseases in nearby communities.
Lithium compounds in finished batteries generally contain lithium in ionic form, which is less reactive than lithium metal and presents fewer flammability hazards. Exposure to ionic lithium, which is present in both anode material and electrolyte salts, has both acute and chronic health effects on the central nervous system.
Cobalt: turning our world blue, not green
Lithium isn’t the only problematic metal in lithium-ion batteries. Cobalt, which can constitute a significant amount of the cathode material, is toxic when inhaled or consumed at above-average levels. Cobalt toxicity can lead to chronic respiratory and cardiovascular diseases and may affect the reproductive system in both men and women. People who mine and process cobalt are at the most acute risk, but as more lithium-ion batteries find their way into waste streams and water supplies, the risk to the public increases.
Much of the world’s cobalt—up to 70% by some estimates—comes from central African nations such as Zambia and the Democratic Republic of the Congo that lack proper safeguards for personal health and the environment. Many small “artisanal” miners are known to take advantage of forced child labor, with up to 40,000 children as young as six years old mining cobalt in the Congo. The mines themselves are often unsafe, suffering from poor ventilation and prone to collapse. Human rights organizations have begun to focus on the cobalt trade in Africa, and cobalt mining has created ongoing environmental damage in countries including Cuba and Australia.
Nickel: guilty by association
The cathode material in some high-density lithium-ion batteries includes as much as 80% nickel. Coal-fired nickel smelters, such as the ones found in Indonesia, release carcinogenic sulfur dioxide into the air, and communities near nickel mines and smelting operations have reported elevated rates of deformities and respiratory problems associated with exposure to pollution. The National Institutes for Occupational Safety and Health in the US have recommended that the permissible exposure limits for nickel compounds be reduced to 0.015 mg/m3, based on evidence of carcinogenicity.
Polymers and solvents: putting workers at risk
The organic liquids used in most electrolyte formulations are both mildly toxic when ingested and can irritate the eyes and skin. Inhaling their vapors may cause nausea, vomiting, or headaches. Overexposure to lithium hexafluorophosphate (LiPF6) salts affects the digestive, circulatory, respiratory, and nervous systems, skin, and bones. Ingestion is the most dangerous path of entry into the body, but inhalation and skin contact can also be harmful.
Polyvinylidene (PVDF) polymers, widely used as binders in lithium-ion batteries, create health hazards during the recycling process. If heated in the absence of oxygen (pyrolysis), PVDF binders release extremely dangerous hydrogen fluoride gas, which can cause blindness on exposure as well as convert to highly corrosive hydrofluoric acid in the presence of moisture. Dissolution using the solvent N-methyl-2-pyrrolidone (NMP) also creates the risk of toxic emissions.
Direct exposure to NMP can also lead to several adverse health effects. The EPA describes NMP as a developmental toxicant, which is a toxin that interferes with growth and development. NMP can irritate the skin and eyes and can make it difficult to breathe by irritating the lungs and respiratory system. Extended exposure to NMP can also cause kidney and liver damage, neurotoxicity, and reproductive toxicity. Any exposure to NMP before or during pregnancy can result in fetal development problems, including decreased fetal weight and even death.
There are few good end-of-life options
The growth of e-waste streams brought on by accelerated consumption trends and shortened device lifespans is poised to become a global-scale environmental issue in the short-term. As the main source of electricity for a broad range of devices, batteries are a significant contributor to total generated e-waste, containing considerable quantities of heavy metals like lead and cadmium, as well as lithium and other contaminants widely regarded as ecotoxic. Furthermore, the wide range of sizes and different compositions between batteries contribute to their improper disposal and make recycling difficult.
Generally, there are three main end-of-life pathways for lithium-ion batteries:
- Disposal, which generally means sending batteries to landfills, is the least preferred option as it leads to material loss, increased environmental risk and health hazards, and waste of economic opportunity. Moreover, stockpiling (and/or landfilling) and shipping end-of-life batteries abroad as a part of end-of-life vehicle wholesale are less preferable options.
- Reuse of EV batteries encompasses remanufacturing and repurposing. Remanufacturing is an opportunity to refurbish retired batteries and use them again in automotive applications after replacing faulty or degraded cells. The main impetus for recycling is to divert materials from landfills, reducing the costs of lithium battery lifecycle, and return strategic and critical materials into the market. The challenges begin with removing batteries from the cars. Handling retired EVs and removing their batteries requires specific knowledge, trained personnel, and specialized tools.
- Recycling processes for lithium batteries are not completely pollution-free activities and introduce risks that adversely affect human health and ecosystem quality. Thus, recycling processes must be thoroughly assessed. Currently, most of the research is focused on GHG emissions, neglecting other emissions and impact categories.
How do we make lithium-ion batteries less toxic?
Making lithium-ion batteries less toxic will be difficult. Lithium-iron-phosphate (LFP / LiFePO4) batteries that eliminate the need for cobalt are a step in the right direction, but remain problematic. The only true option is to move away from lithium-based chemistries completely. Technologies currently under development, such as the one being developed by Alsym Energy, leverage metals and materials that are dramatically less toxic, or inherently non-toxic. These batteries should pose fewer risks across every step of the battery lifecycle, from sourcing to manufacture to disposal.