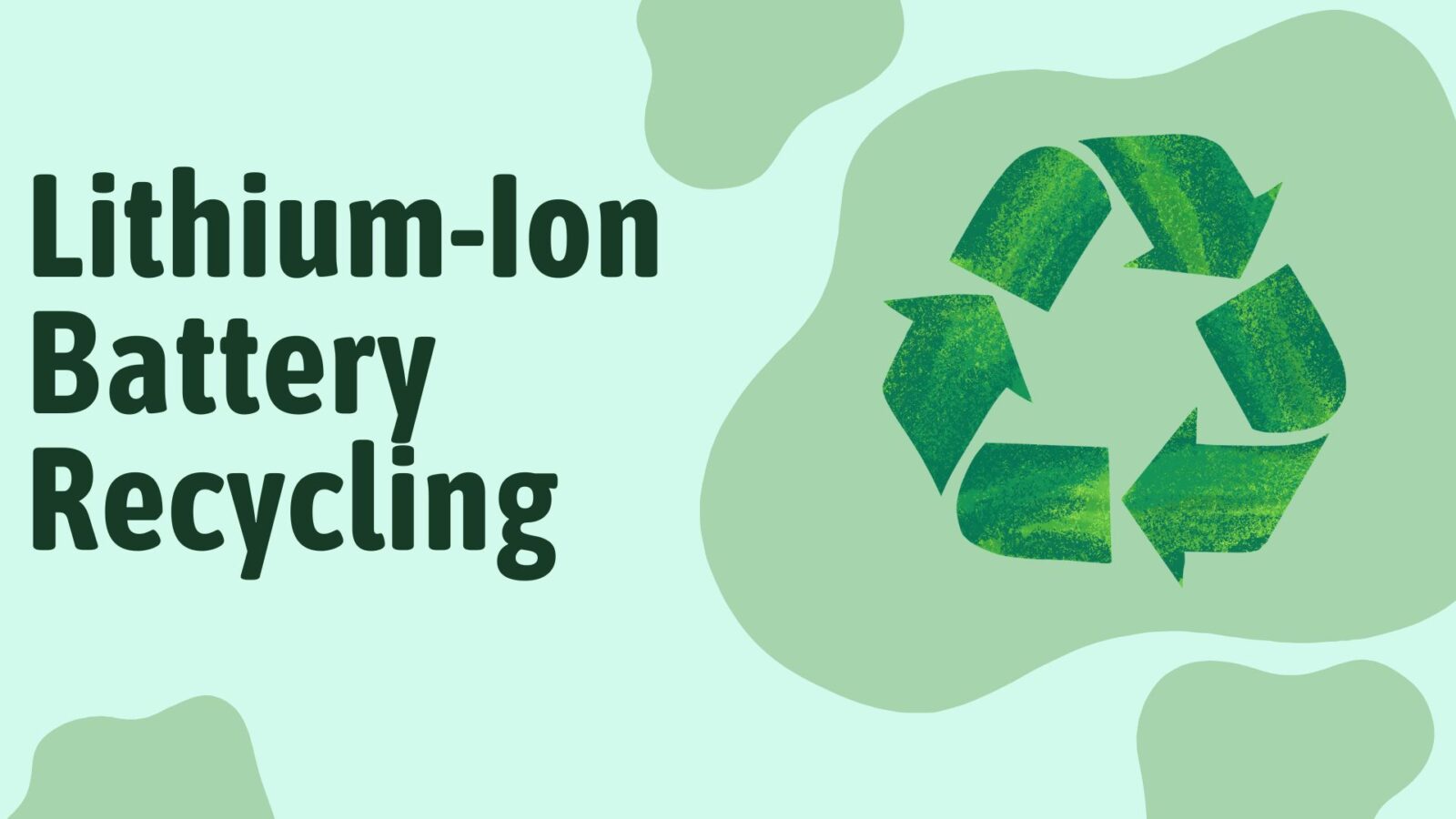
As the demand for electric vehicles increases, so does the need for lithium-ion battery (LIB) recycling. It may seem like current recycling technologies are highly effective at first glance; however, critical studies using lifecycle analysis (LCA) show that several factors affect both potential economic and environmental gains of recycled lithium-ion batteries.
Lithium Battery Recycling – Can Lithium Batteries be Recycled?
Lithium batteries can be recycled. However, no single process for recycling lithium-ion batteries combines low environmental impact and energy cost with high metal yields. Instead, the multiple processes involve a series of tradeoffs that seek to reduce the net environmental impact of battery disposal but can never reach net zero.
This is why Alsym’s battery materials have been purposefully selected to eliminate toxicity risks and be easily recyclable. With no lithium, cobalt, or organic electrolytes, Alsym batteries are safer to manufacture, safer to use, and safer to recycle. And that’s good for everyone.
Lithium Ion Battery Recycling Process
The lithium battery recycling process combines several intermediate recycling technologies. This includes dismantling spent batteries, physical/chemical treatments, and hydrometallurgical/pyrometallurgical steps to recover valuable materials with high purity. Each of these steps has its underlying challenges.
Traditional lithium-ion battery designs don’t consider safe and efficient disassembly, which means taking batteries apart can generate dust. These airborne particles (many less than 10 microns in size) can contain toxic elements including arsenic, chromium, cobalt, and lead that contribute to respiratory and cardiovascular diseases, and may settle on the ground where they pollute the soil. Furthermore, batteries—especially ones that have been damaged or experienced thermal runaway—often release extremely poisonous and/or flammable gasses such as hydrogen, sulfur dioxide, and hydrogen fluoride upon venting.
- Pyrometallurgical processes involve temperatures as high as 1,000 C. Lithium is lost as slag and is difficult to extract, even from post-processing. Other concerns include incinerated plastics, hazardous slags, and toxic gas emissions. These processes involve an intermediate “black mass” which contains hazardous substances such as alkyl fluor phosphates that pose significant threats to human health. Furthermore, the processes may contribute to ozone layer depletion and global warming.
- Hydrometallurgical processes (such as acid leaching) are more efficient than pyrometallurgical processes. They cost less and produce fewer greenhouse gas emissions, but require strong mineral acids that create acidic wastewater and toxic gases that can harm people, plants, and wildlife. Non-regulated disposals of leachates into landfills can cause severe environmental harm, especially due to the release of transition metals containing nanomaterials. Moreover, specific battery chemistries such as lithium-iron-phosphate (LFP) can deplete abiotic resources.
- Alkali leaching can be used instead of acid leaching in some situations. This process depends on the chelation of ammonium ions and metal ions; however, not all such complexes are water-soluble, meaning this approach does not apply to all cathode materials. Bioleaching is another experimental method that uses bacterial/fungal processes to produce acid-type leaching. Studies show great environmental benefits, but bioleaching is very inefficient and isn’t ready for commercialization.
- Purification is an important part of the recycling process. Impurities such as aluminum, copper and iron are often found in the extracted materials. These metals must be removed, as resynthesized cathode performance is very sensitive to constituent elements. Leachate will contain transition metal ions (Ni2+, Co2+, Mn2+ for NCM and Fe2+ for LFP) and Li+ ions, both of which are precipitated separately. It’s difficult to avoid co-precipitation of transition metal ions due to their similar properties, making the metal extraction process more complex and expensive. Other methods for metal extraction also have their own limitations; for example, electrodeposition requires a lot of electricity and is not widely used for that reason.
While lithium-ion batteries have revolutionized our world, their complex and environmentally challenging recycled lithium-ion battery process paints a different picture. Alsym’s innovative battery technology offers a future-proof solution. By eliminating problematic materials like lithium and cobalt, and utilizing inherently non-toxic and non-flammable components, Alsym not only prioritizes safety and performance in its batteries but also simplifies and streamlines the recycling process. This ultimately contributes to a more sustainable and healthy future for everyone, one where clean energy and responsible environmental practices go hand-in-hand.
- Written by Dr. Nikhil Koratkar, co-founder of Alsym Energy, John A. Clark and Edward T. Crossan Chair Professor in Engineering at Rensselaer Polytechnic Institute (RPI)